H11 Hot Work Tool Steel
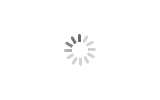
- Shizhang Steel
- China
- 7-35days
- 500 Tons/Month
AISI H11 die steel is often used for highly stressed structural parts such as aircraft landing gear. H11 steel resistssoftening at temperatures up to 537°C while retaining good ductility and toughness even atstrength levels on the order of 275 ksi. Tools for hot forging of light metal. Pressure die castingtools. Dies, mandrels, punchers, knives, moulds. This grade can be water cooled.
Product Name: HOT WORK TOOL STEEL---AISI H11
Similar steel grades:
AISI | H11 |
W. Nr. | 1.2343 |
DIN | X37CrMoV5 |
JIS | - |
GB/T1299-2000 | 4Cr5MoSiV |
ISO | X37CrMoV5-1 |
Chemistry (in %)
C | Cr | Mo | Si | V | Mn | P | S |
0.33-0.43 | 4.75-5.50 | 1.1-1.6 | 0.8-1.2 | 0.3-0.6 | 0.2-0.5 | ≤0.03 | ≤0.03 |
Principal Feature:
AISI H11 tool steel is a 5% chromium hot work steel that is characterized by excellent impact toughness. H11 steel contains less vanadium than the widely-used H13 hot work tool steel. AISI H11 die steel is a deep-hardening, air-hardening steel that exhibits minimal size change during heat treatment. H11 steel has good resistance to thermal fatigue cracking (heat checking) and excellent resistance to gross cracking and thermal shock when water cooled in service. AISI H11 die steel is recommended for hot tooling applications where maximum resistance to cracking is required.
Typical Application:
H11 tool steel is typically applied in high-load hot work scenarios. It is well-suited for manufacturing high-speed hammer forging dies, die casting,aluminum and magnesium alloy hot forging dies, and black metal forging dies . Its applications also extend to hot work forging and extrusion dies, as well as helicopter rotor blades, where high toughness and hardness are required . The steel's excellent resistance to thermal fatigue, good hot hardness, and excellent machinability make it a preferred choice in these applications . To enhance its properties for longer life and higher design accuracy, H11 steel can undergo various heat treatment processes .
Heat Treatment:
Forge: at 1050℃-1095℃ Cool slowly and anneal then.
Annealing: at 843℃-898℃ Cool slowly in furnace
Stress Relieving: heat slowly to 566-676℃, and then cool in still air.
Hardening: Preheat to 815 ℃ and then heat to 1010℃ and hold for 15 to 40 minutes. Air cool (air quench)
Size available:
Bars | Turned | Dia 20-800mm |
Black | Dia 20-800mm | |
Flats | Milled | T:50-300 W: 200-710mm |
Black | T: 8-300 W: 200-710mm |